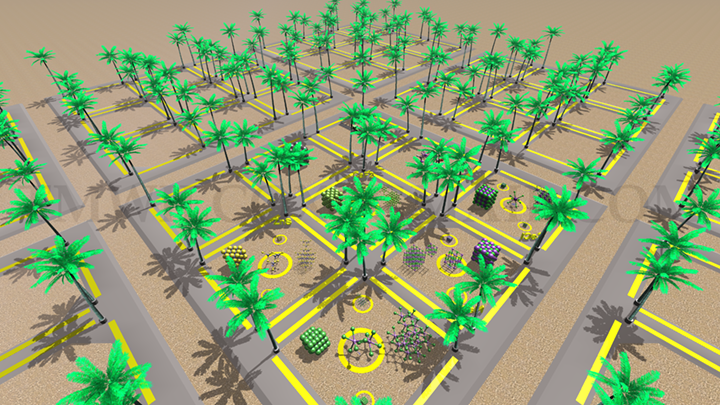
- Case Study -
3D SCANNER
I needed an automated 3D scanner to digitally copy large objects. Art students and faculty wanted something big enough to scan people and clothing. A nursing professor imagined rapid skin cancer screening. Made of engineered wood cut with a computerized router, the scanner's rigid framework enables precise motion control. Visitors experienced these life-size, animated models with virtual reality at the VR Innovation Gallery.
Digital prototypes readily spawn divergent concepts and sometimes surprisingly impractical designs. I imagined the scanner scaled down to desktop size for digitizing small objects. Despite its many pieces, I considered scanner kits of laser-cut clear acrylic.
Design students wanted to digitize costumed actors at the University of Virginia across the Blue Ridge in Charlottesville, so I adapted another prototype for transportability with lightweight aluminum tubing. Speeding up the visualization process, I used a free 3D model of an outdated film camera that's good enough for concept mockups. The downloaded camera model came with a Creative Commons license.
The scanner uses LIDAR or photogrammetry or both to generate point clouds. LIDAR emits a low intensity laser beam reflected by a scanned object. Photogrammetry employs one or more digital cameras to create an all-encompassing, photographic texture map applied to a polygon mesh derived from a point cloud. Designed for real-world applications, my 3D scanner also demonstrated advanced prototyping at the Ice House Innovation Space.
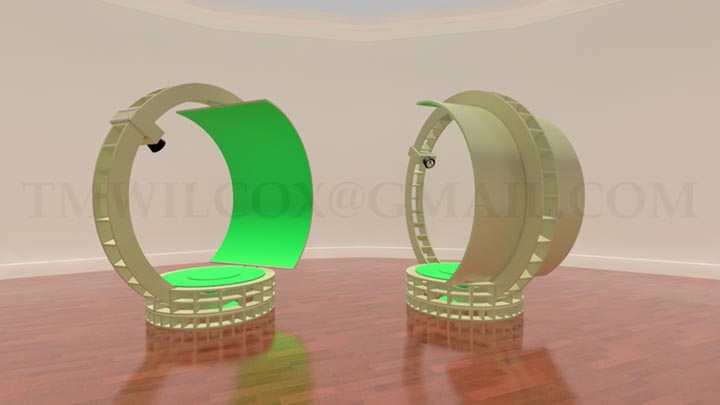
I needed an automated 3D scanner to digitally copy large objects. Art students and faculty wanted something big enough to scan people and clothing. A nursing professor imagined rapid skin cancer screening. Made of engineered wood cut with a computerized router, the scanner's rigid framework enables precise motion control. Visitors experienced these life-size, animated models with virtual reality at the VR Innovation Gallery.
Digital prototypes readily spawn divergent concepts and sometimes surprisingly impractical designs. I imagined the scanner scaled down to desktop size for digitizing small objects. Despite its many pieces, I considered scanner kits of laser-cut clear acrylic.
Design students wanted to digitize costumed actors at the University of Virginia across the Blue Ridge in Charlottesville, so I adapted another prototype for transportability with lightweight aluminum tubing. Speeding up the visualization process, I used a free 3D model of an outdated film camera that's good enough for concept mockups. The downloaded camera model came with a Creative Commons license.
The scanner uses LIDAR or photogrammetry or both to generate point clouds. LIDAR emits a low intensity laser beam reflected by a scanned object. Photogrammetry employs one or more digital cameras to create an all-encompassing, photographic texture map applied to a polygon mesh derived from a point cloud. Designed for real-world applications, my 3D scanner also demonstrated advanced prototyping at the Ice House Innovation Space.
I needed an automated 3D scanner to digitally copy large objects. Art students and faculty wanted something big enough to scan people and clothing. A nursing professor imagined rapid skin cancer screening. Made of engineered wood cut with a computerized router, the scanner's rigid framework enables precise motion control. Visitors experienced these life-size, animated models with virtual reality at the VR Innovation Gallery.
Digital prototypes readily spawn divergent concepts and sometimes surprisingly impractical designs. I imagined the scanner scaled down to desktop size for digitizing small objects. Despite its many pieces, I considered scanner kits of laser-cut clear acrylic.
Design students wanted to digitize costumed actors at the University of Virginia across the Blue Ridge in Charlottesville, so I adapted another prototype for transportability with lightweight aluminum tubing. Speeding up the visualization process, I used a free 3D model of an outdated film camera that's good enough for concept mockups. The downloaded camera model came with a Creative Commons license.
The scanner uses LIDAR or photogrammetry or both to generate point clouds. LIDAR emits a low intensity laser beam reflected by a scanned object. Photogrammetry employs one or more digital cameras to create an all-encompassing, photographic texture map applied to a polygon mesh derived from a point cloud. Designed for real-world applications, my 3D scanner also demonstrated advanced prototyping at the Ice House Innovation Space.