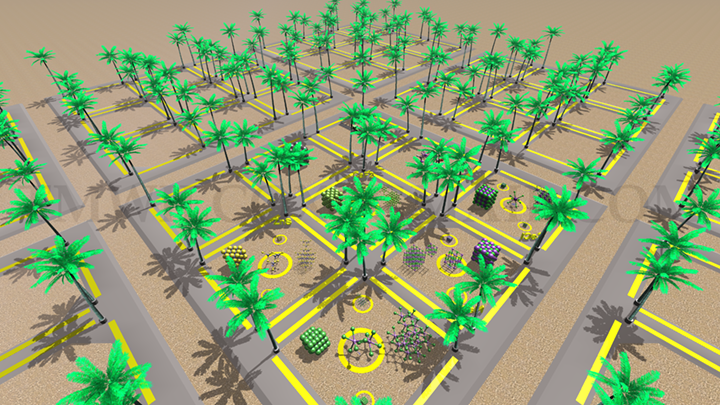
- Case Study -
FRAME CONNECTOR
Lab frames organize equipment in laboratories and workshops. Designed for desktop 3D printing, my spherical frame connector demonstrates digital prototyping with virtual reality at the VR Innovation Gallery. Rapid prototypes were on display at the Ice House Innovation Space.
It seemed easy enough at first, printing hundreds of small objects. While faster printers are on the way, an early fused deposition modeling (FDM) machine took over fifteen hours to print twenty-seven connectors. When a chemistry professor noticed my prototype resembles a ball-and-stick model, I proposed giant crystal lattice models in a virtual reality teaching and learning environment.
These were early forays into desktop 3D printing at the university. I used this rig to stress test different filaments, and various infill densities, defined as a hollowness percentage. Ideally, concept visualization combines digital and physical models, demonstrating wide-ranging design characteristics.

Lab frames organize equipment in laboratories and workshops. Designed for desktop 3D printing, my spherical frame connector demonstrates digital prototyping with virtual reality at the VR Innovation Gallery. Rapid prototypes were on display at the Ice House Innovation Space.
It seemed easy enough at first, printing hundreds of small objects. While faster printers are on the way, an early fused deposition modeling (FDM) machine took over fifteen hours to print twenty-seven connectors. When a chemistry professor noticed my prototype resembles a ball-and-stick model, I proposed giant crystal lattice models in a virtual reality teaching and learning environment.
These were early forays into desktop 3D printing at the university. I used this rig to stress test different filaments, and various infill densities, defined as a hollowness percentage. Ideally, concept visualization combines digital and physical models, demonstrating wide-ranging design characteristics.
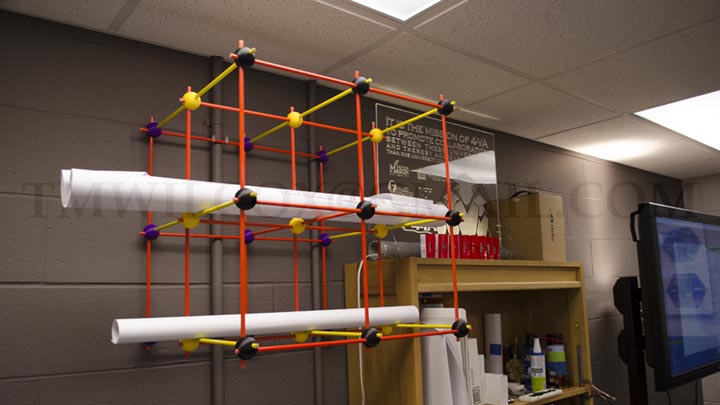
It seemed easy enough at first, printing hundreds of small objects. While faster printers are on the way, an early fused deposition modeling (FDM) machine took over fifteen hours to print twenty-seven connectors. When a chemistry professor noticed my prototype resembles a ball-and-stick model, I proposed giant crystal lattice models in a virtual reality teaching and learning environment.
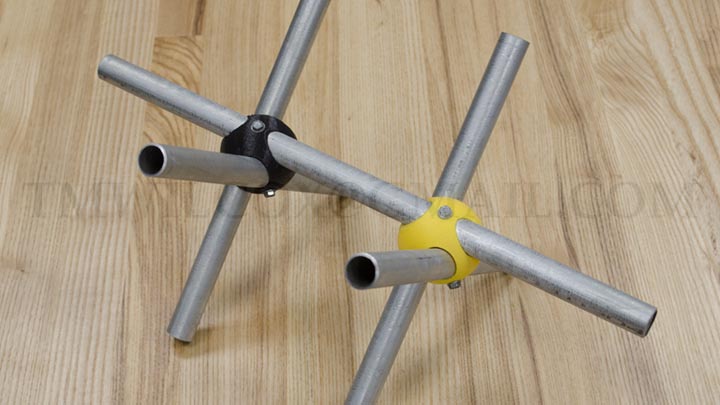
These were early forays into desktop 3D printing at the university. I used this rig to stress test different filaments, and various infill densities, defined as a hollowness percentage. Ideally, concept visualization combines digital and physical models, demonstrating wide-ranging design characteristics.